The evolution of mankind is closely related to our ability to invent and manufacture various items that made our lives easier, more comfortable and helped us work more efficiently. The industrial revolution helped us move from artisan production of a small number of items to mass production of identical items. Now AR/VR technology is ready to help the manufacturing industry make the leap to a new era, where there are no boundaries to the way people can develop product concepts, test their viability and finally build them.
AR/VR Technology – the Missing Link in the Future Evolution of Manufacturing
Mass manufacturing is already highly automated. Manual labor is virtually absent from all the phases of building the parts making up a finished product and putting them together. However, this does not mean that we have reached the pinnacle of development and there is nothing else to be done to modernize and improve the manufacturing industry.
Starting with the way products are designed and ending with the way workers are trained to work with robots and inspect finished items for quality assurance, AR/VR technology is the missing link this industry needed to move to the next era, dubbed by specialists Industry 4.0.
How AR and VR Reshape the Manufacturing Industry
1. Product Design
The traditional way of creating a new product was drawing a sketch on paper. The computer era brought about advanced 3D graphics software, allowing product designers and engineers to visualize a tridimensional product model from various angles and even look inside it and watch various mechanisms and components at work.
Virtual reality is taking things one step further: product designers can interact with a holographic model of the product, virtually touch its parts, simulate various ways of using it, create best and worst case scenarios and identify potential design flaws.
This is already being done by Ford Motor Company. For some years now, the iconic US car manufacturer has equipped its engineers and product designers with VR headsets and specialized software to enable them to create better cars. Here is a demonstration of how Ford cars are designed:
2. Assembly Made Simpler
Another key phase in the manufacturing process is the final assembly of a complex product. Once again, we revert to cars, because they consist of so many parts and it is absolutely vital to assemble them correctly.
One of the best-known European car manufacturers, Volvo, has established a partnership with Microsoft HoloLens, a mixed reality HMD, to take their manufacturing and assembly processes to the next level.
Volvo shows how their cars are put together using Microsoft HoloLens: assembly workers are permanently guided by superimposed visuals in placing every part of the automobile and testing that it is properly working.
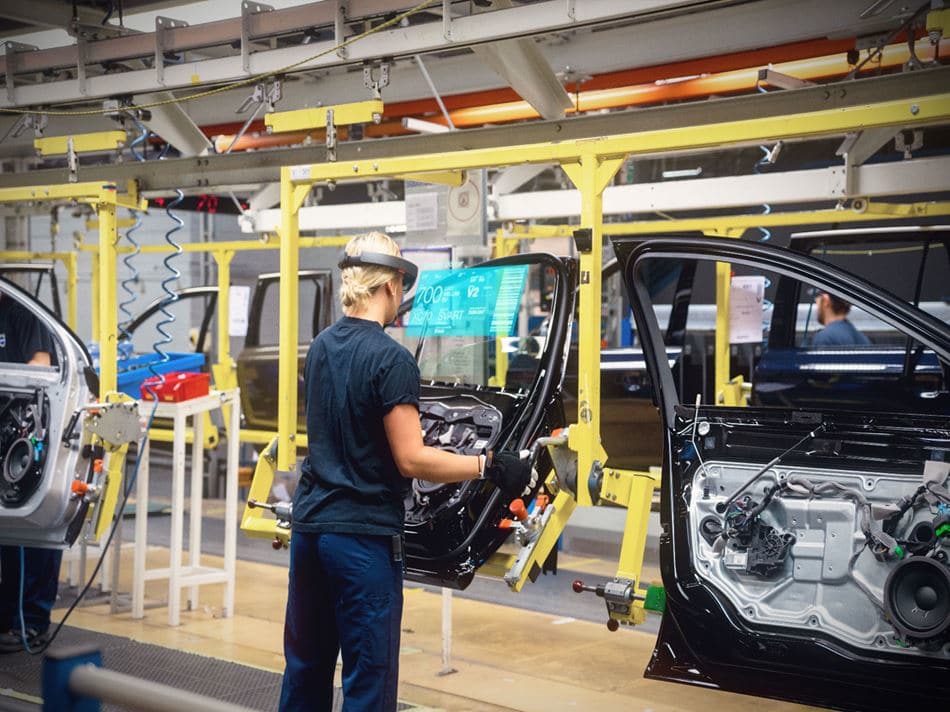
3. Uniform Employee Training in a Global Market
Successful companies expand globally by opening branch offices all over the world. One of the challenges of being a global corporation is maintaining the brand image and values in all the operational aspects. Proper employee training is part of maintaining brand values.
Traditional training, where employees sit in a training room to take theoretical classes and then engage in practice, is very impractical for employees located all over the world. But AR/VR technology can bring people together in a simulated holographic environment and teach them the same skills with the same level of professionalism.
This is what Volkswagen is currently doing: using virtual reality to make sure all their employees know and apply the same work procedures in their daily activities.
4. Quality Assurance
No product reaches the store shelves without passing through the quality check inspection. This is a detailed and time consuming activity, but it is mandatory. In recent years, manufacturing companies across the world have been looking for ways to make the quality assurance process more efficient and productive.
Using AR technology, an experiment conducted by the Faculty of Technical Communication at the THM University of Applied Sciences in Germany, indicated the viability of this new technology as driving force for progress in the field.
5. Ongoing Maintenance
Complex products need to be maintained during their useful life. Although it is not a part of the manufacturing process per se, product maintenance technically belongs to the manufacturing industry. It needs skilled workers who known how the product is supposed to work, ways in which it may malfunction and know exactly what part they need to fix or replace.
One of the largest manufacturers of elevators in the world, thyssenkrupp, is currently using augmented reality technology deployed via Microsoft HoloLens devices, to guide maintenance teams during the preventive inspection and repair activities.